This is an excerpt from the RX4 Chassis Manual addendum that can be downloaded here for easy printing.
RX4 Drive Train Tutorial
General Service Information
- Keep grease and oil off brake pads and rotors.
- Discard contaminated brake pads and clean rotors with degreaser.
- Brake dust may contain asbestos fibers.
- Do not clean brake dust with compressed air.
- Do not allow water, dirt or other contaminates to enter the hydraulic brake system.
- If brake lever or pedal feels spongy, system needs to be bled.
- Only use fresh DOT 3 or 4 brake fluid from a sealed container
- After servicing wheels, brakes or suspension always verify brake function before riding.
- When servicing wheels, suspension or steering, lift motorcycle with suitable work stand.
EMISSION RELATED ITEMS MILES(x)1K | FIRST SERVICE 500 | 2.5K | 5K | 7.5K | 10K | 12.5 | 15K | 17.5 | 20K | |
---|---|---|---|---|---|---|---|---|---|---|
FUEL LINE | * | I | I | I | I | I | ||||
FUEL FILTER | * | R | R | R | R | |||||
THROTTLE OPERATION | * | I | I | I | I | I | ||||
AIR CLEANER | I | I | I | I | ||||||
SPARK PLUG | I | I | R | I | ||||||
VALVE CLEARANCE | * | I | I | I | I | |||||
ENGINE OIL | R | R | R | R | R | R | R | R | R | |
ENGINE OIL FILTER | R | R | R | R | R | R | R | R | R | |
RADIATOR COOLANT | I | I | R | I | ||||||
COOLING SYSTEM | * | I | I | I | I | |||||
EVAPORATIVE EMISSION CONTROL SYSTEM | * | I | |
I | I | I | ||||
NON-EMISSION RELATED ITEMS MILES(x)1K |
FIRST SERVICE
500
| 2.5K | 5K | 7.5 | 10K | 12.5 | 15K | 17.5 | 20K | |
DRIVE CHAIN | I | I | I | I | I | I | I | I | I | |
BATTERY | I | I | I | I | I | I | I | I | I | |
BRAKE FLUID | I | I | I | I | I | R | I | I | ||
BRAKE PAD WEAR | I | I | I | I | I | I | I | I | ||
BRAKE SYSTEM | I | I | I | I | I | |||||
BRAKE LIGHT SWITCH | * | I | I | I | I | I | ||||
HEADLIGHT AIM | * | I | I | I | I | I | ||||
CLUTCH SYSTEM | I | I | I | I | I | |||||
SIDE STAND | I | I | I | I | I | |||||
SUSPENSION | * | I | I | I | I | I | ||||
NUTS, BOLTS, FASTENERS | I | I | I | I | I | I | I | I | I | |
WHEELS/TIRES | ** | I | I | I | I | I | I | I | I | I |
STEERING HEAD BEARINGS | ** | I | I | I | I | I |
Specifications
Standard Torque Values
Bolt Size | Torque |
---|---|
5 mm 6 mm 8 mm 10 mm 12 mm |
5.2 mn (3.8 ft lbs) 10 nm (7 ft lbs) 22 nm (16 ft lbs) 34 nm (25 ft lbs) 54 nm (40 ft lbs) |
Front Wheel
Rim- 2.15 x 19 in
Tire- 110/80R19,
Cold tire pressure- 36 psi
Wheel runout- 2 mm (0.08 in) Axial/Radial
Axle torque- 106 nm (78 ft lbs)
Axle runout- 0.02 mm (0.008 in)
Spoke nipple size- 6 mm
Spoke nipple torque- 3.7 nm (32.7 in lbs)
Rear wheel
Rim- 4.25 x 17 in
Tire- 150/70R17
Cold tire pressure- 36 psi
Wheel runout- 2 mm (0.08 in) Axial/Radial
Axle torque- 106 nm (78 ft lbs)
Axle runout- 0.02 mm (0.008 in)
Spoke nipple size- 6 mm
Spoke nipple torque- 3.7 nm (32.7 in lbs)
Rear Sprocket- 44 teeth
Chain- 530 x 108 links
Drive chain slack- 25-35 mm (1.0-1.4 in)
Front Fork
Stanchion diameter- 41 mm
Suspension travel- 130 mm (5.1in)
Rebound dampening adjustment- 16 clicks
Fork oil weight- 5w suspension fluid
Rear Shock
Eye to eye length- 44 cm (17.3 in)
Suspension travel- 120 mm (4.7 in)
Rebound dampening adjustment- 6 clicks
Damper gas pressure- 150 psi
Front Brake
Minimum pad thickness- 1 mm (wear indicator)
Minimum rotor thickness- 3 mm
Mounting bolt torque- (22 ft lbs)
Brake fluid- DOT 3 or 4
Rear Brake
Minimum pad thickness- 1 mm (wear indicator)
Minimum rotor thickness- 3 mm
Mounting bolt torque- (22 ft lbs)
Brake fluid- DOT 3 or 4
Stanchion diameter- 41 mm
Suspension travel- 130 mm (5.1in)
Rebound dampening adjustment- 16 clicks
Fork oil weight- 5w suspension fluid
Rear Shock
Eye to eye length- 44 cm (17.3 in)
Suspension travel- 120 mm (4.7 in)
Rebound dampening adjustment- 6 clicks
Damper gas pressure- 150 psi
Front Brake
Minimum pad thickness- 1 mm (wear indicator)
Minimum rotor thickness- 3 mm
Mounting bolt torque- (22 ft lbs)
Brake fluid- DOT 3 or 4
Rear Brake
Minimum pad thickness- 1 mm (wear indicator)
Minimum rotor thickness- 3 mm
Mounting bolt torque- (22 ft lbs)
Brake fluid- DOT 3 or 4
Troubleshooting
Hard steering
- Steering stem adjusted to tight
- Damaged steering head bearings
- Inadequate lubrication in steering head bearings
- Low tire pressure
Steers to one side or does not track straight
- Front wheel installed incorrectly
- Misaligned rear wheel
- Loose axle
- Loose front axle pinch bolts
- Worn wheel bearings
- Worn swingarm bearings
- Bent axle
- Bent fork tube
Wheels wobble
- Loose axle
- Loose front axle pinch bolt
- Wheels out of balance
- Faulty tire
- Bent rim
- Bent spokes
- Worn wheel bearings
Brake lever/pedal soft of spongy
- Air in brake hydraulic system
- Leak in hydraulic brake system
- Misadjusted brake lever/pedal
- Worn seals in master cylinder
- Worn seals in caliper
- Clogged passages in brake hydraulic system
- Low fluid
- Contaminated brake pads or rotors
- Warped rotor
- Bent or worn brake lever/pedal
Drive train
Adjust drive chain
For maximum service life, drive chain should be cleaned and lubricated every 500 mile or as needed. Chain adjustment should be performed with motorcycle in neutral and on a suitable service stand. Inspect drive chain for damage and wear. Replace chain that has damaged rollers, rust or excessive wear. Replacing a chain on worn sprockets will accelerate wear of the chain. Use 80/90w gear oil or commercially available chain lube. Wipe off excessive lubrication and avoid contaminating brake rotors or pads.
Step 1: Place the rear of the motorcycle on suitable work stand.
Step 2: Place the transmission in neutral
Step 3: Cautiously spin rear wheel while measuring the slack in the middle of the bottom chain run halfway between the sprockets.
Step 4: Stop and measure the chain at its tightest spot
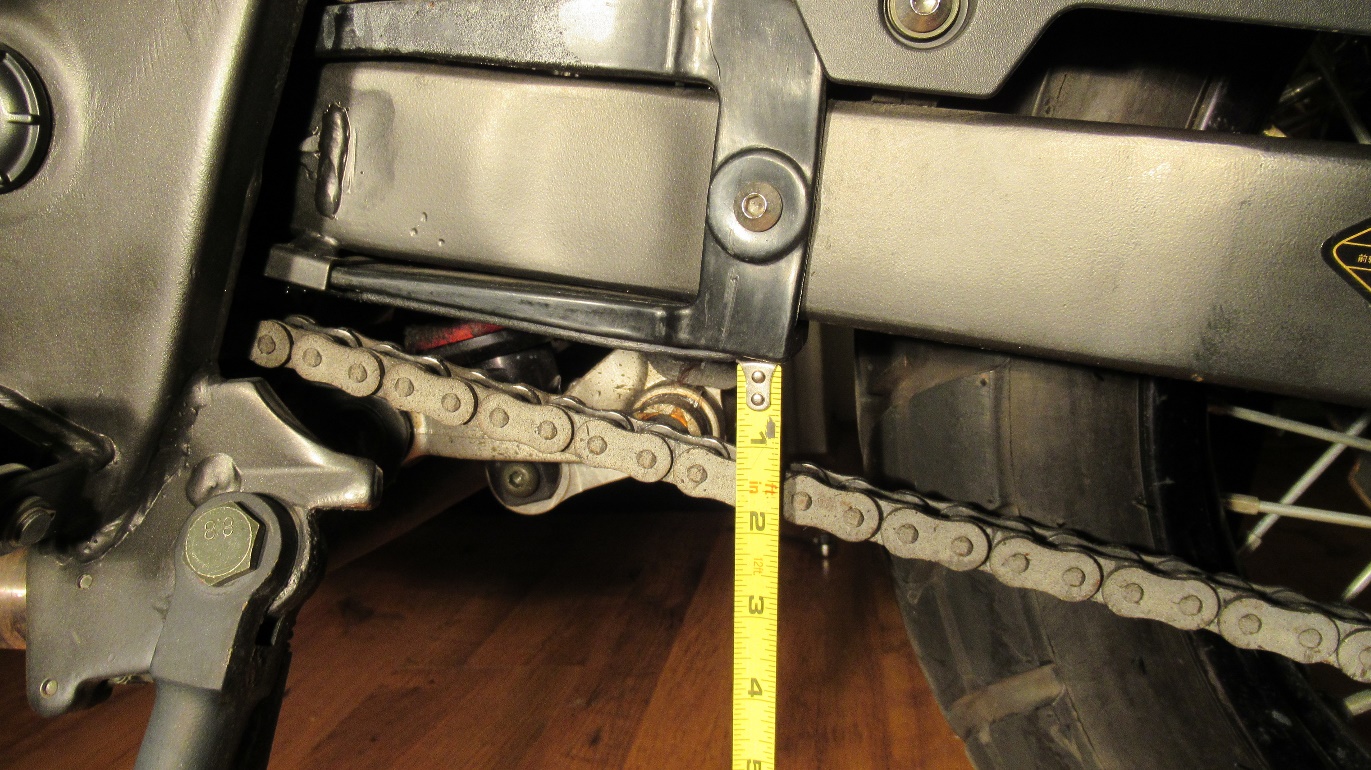
Step 5: Chain Slack: 25 – 35 mm. Excessive slack may cause frame and swingarm damage
Step 6: If the chain is out of adjustment loosen the axle nut and adjuster locknuts. Turn the adjuster bolts to move the adjuster brackets
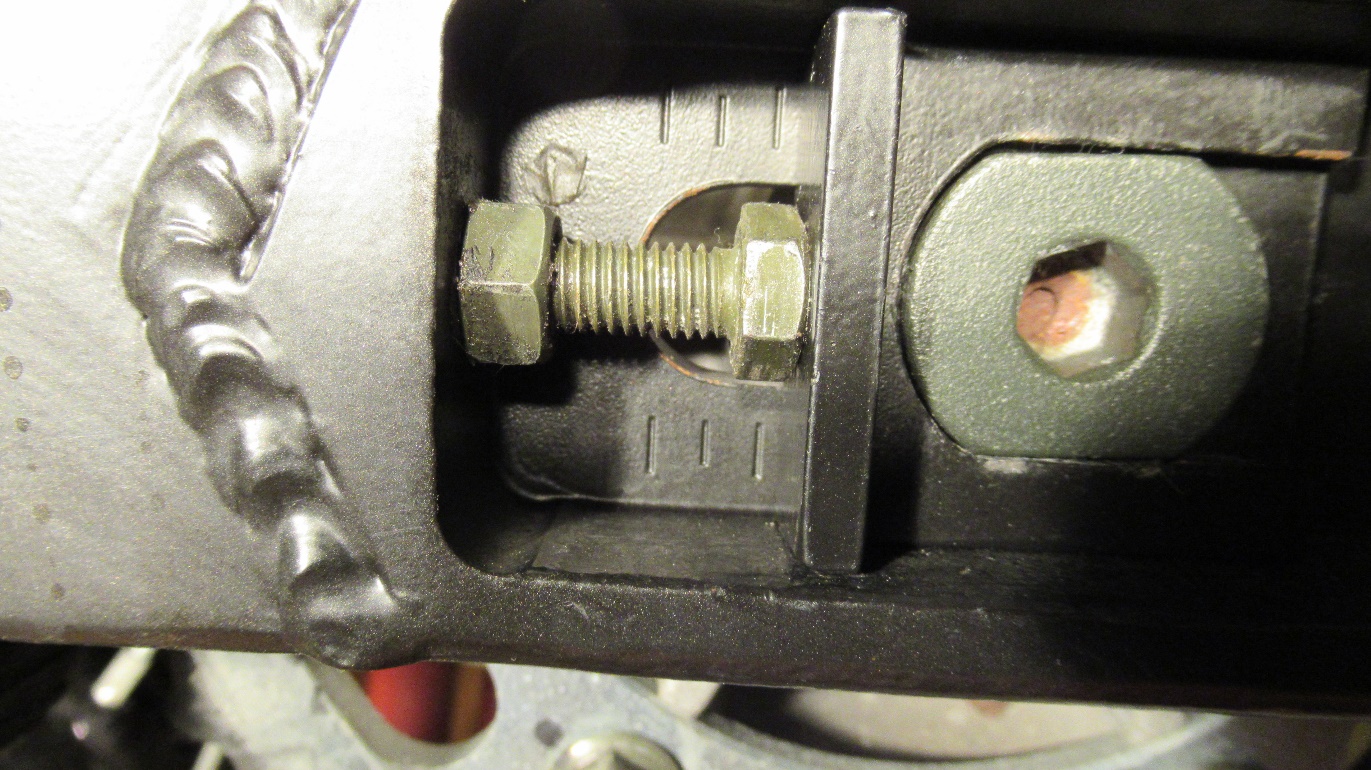
Step 7: Use the index marks on the swingarm to verify that both sides are being adjusted equally.
Step 8: Torque axle nut to 106 nm (78 ft lbs)
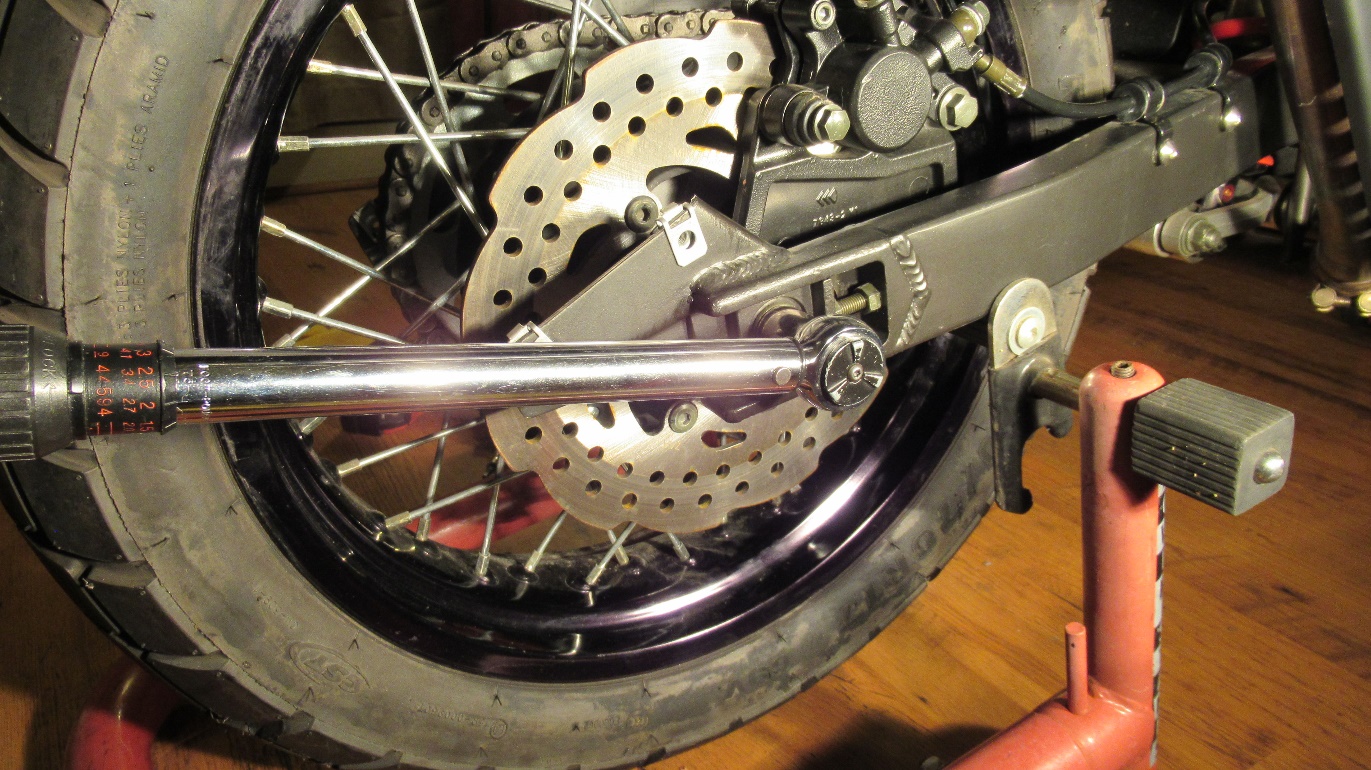
Step 9: After torqueing axle, lightly seat adjuster bolts against adjuster brackets and tighten locknut.
Adjust drive chain
For maximum service life, drive chain should be cleaned and lubricated every 500 mile or as needed. Chain adjustment should be performed with motorcycle in neutral and on a suitable service stand. Inspect drive chain for damage and wear. Replace chain that has damaged rollers, rust or excessive wear. Replacing a chain on worn sprockets will accelerate wear of the chain. Use 80/90w gear oil or commercially available chain lube. Wipe off excessive lubrication and avoid contaminating brake rotors or pads.
Step 1: Place the rear of the motorcycle on suitable work stand.
Step 2: Place the transmission in neutral
Step 3: Cautiously spin rear wheel while measuring the slack in the middle of the bottom chain run halfway between the sprockets.
Step 4: Stop and measure the chain at its tightest spot
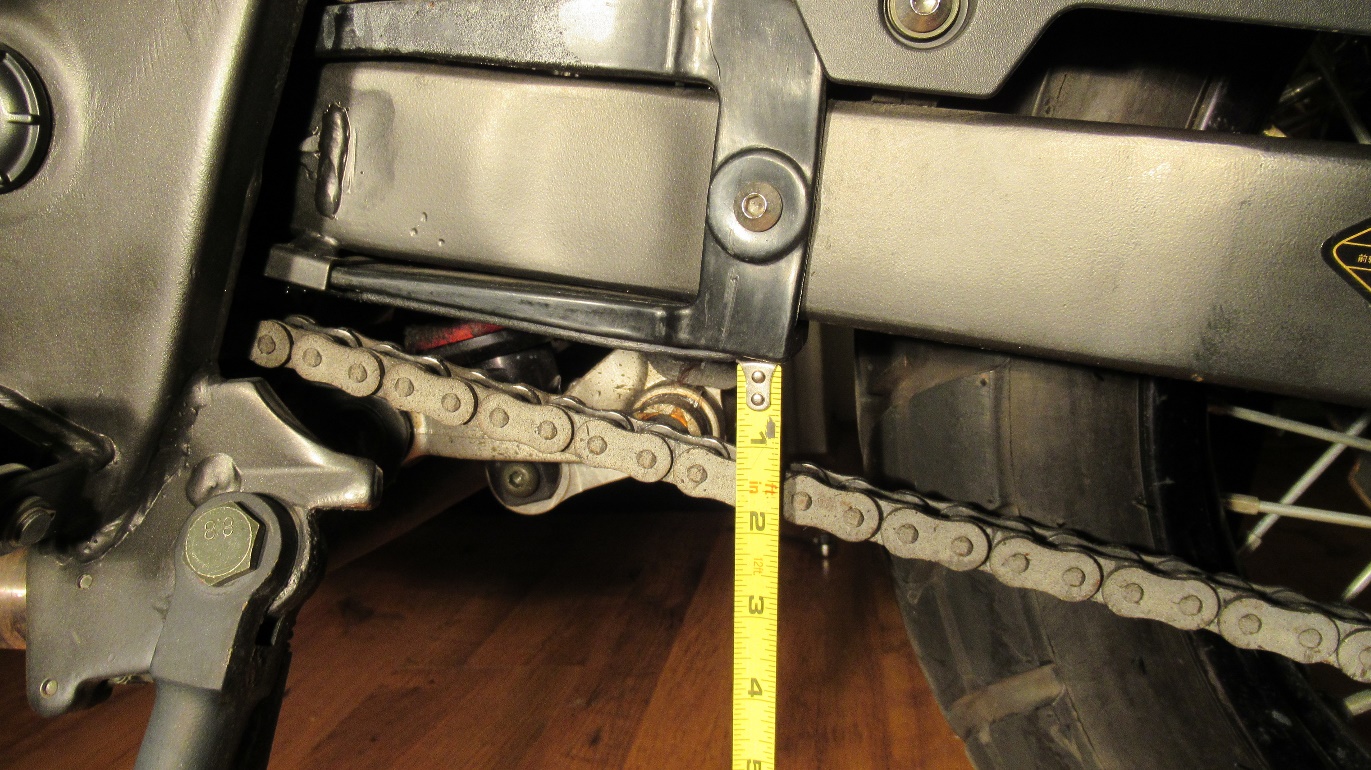
Step 5: Chain Slack: 25 – 35 mm. Excessive slack may cause frame and swingarm damage
Step 6: If the chain is out of adjustment loosen the axle nut and adjuster locknuts. Turn the adjuster bolts to move the adjuster brackets
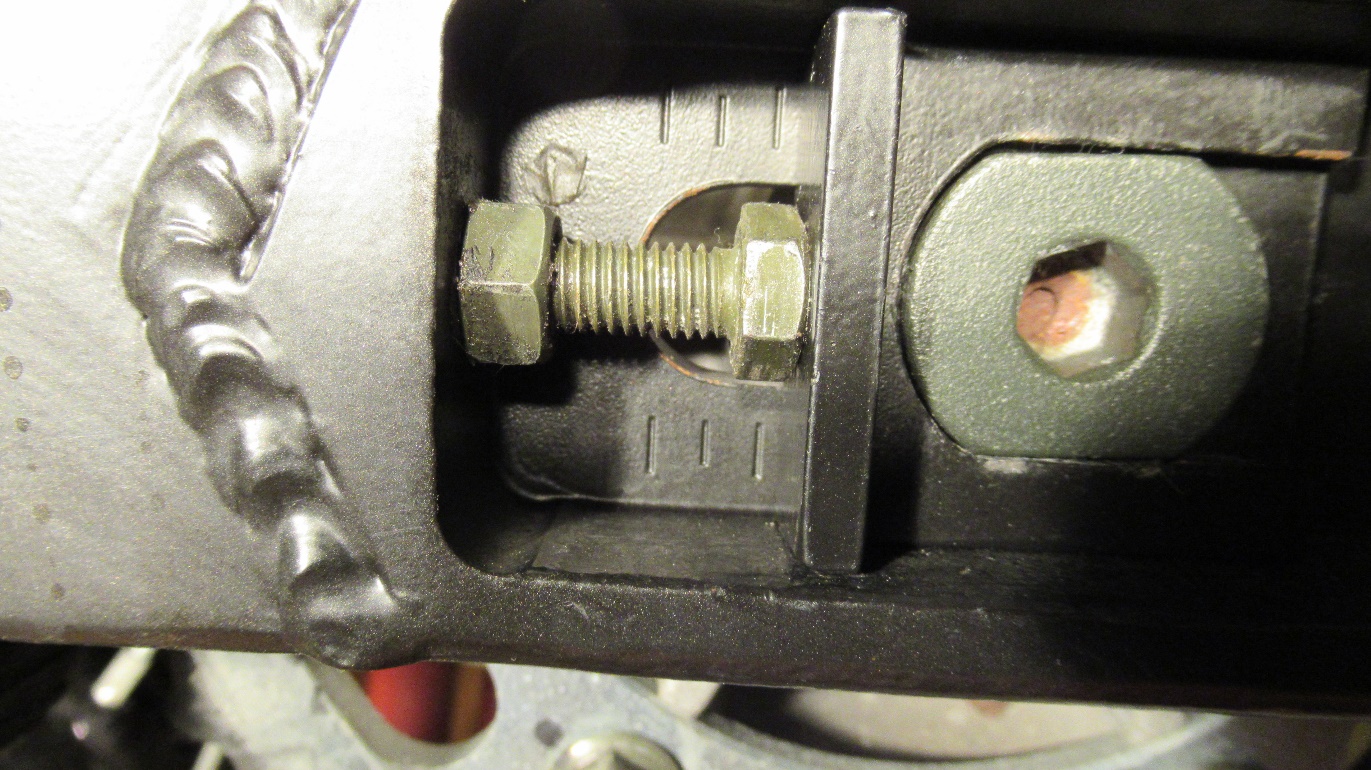
Step 7: Use the index marks on the swingarm to verify that both sides are being adjusted equally.
Step 8: Torque axle nut to 106 nm (78 ft lbs)
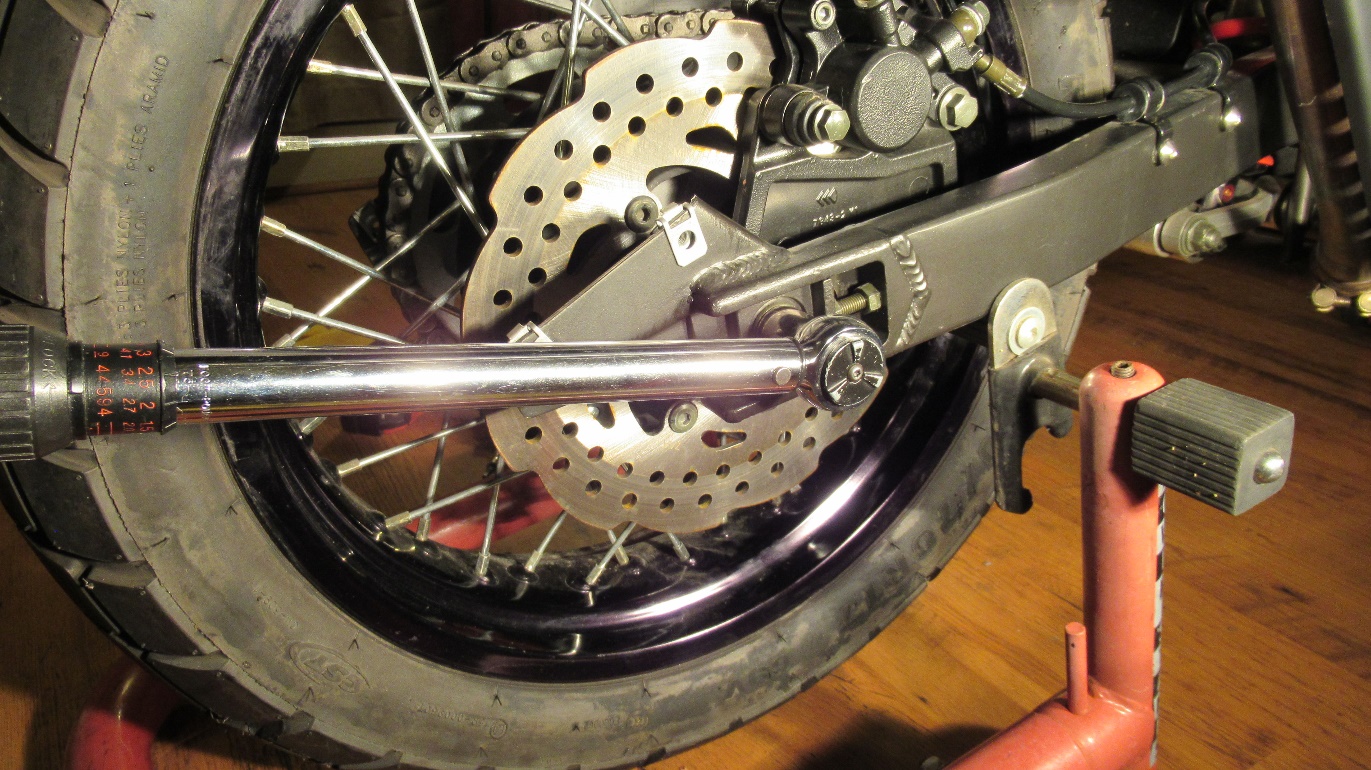
Step 9: After torqueing axle, lightly seat adjuster bolts against adjuster brackets and tighten locknut.